Solutions
Innovative, alternative solutions to get your products to market more quickly.
- CDT Solutions
- Prototyping
- Project Management
- Precision Tooling
- Validation Activities
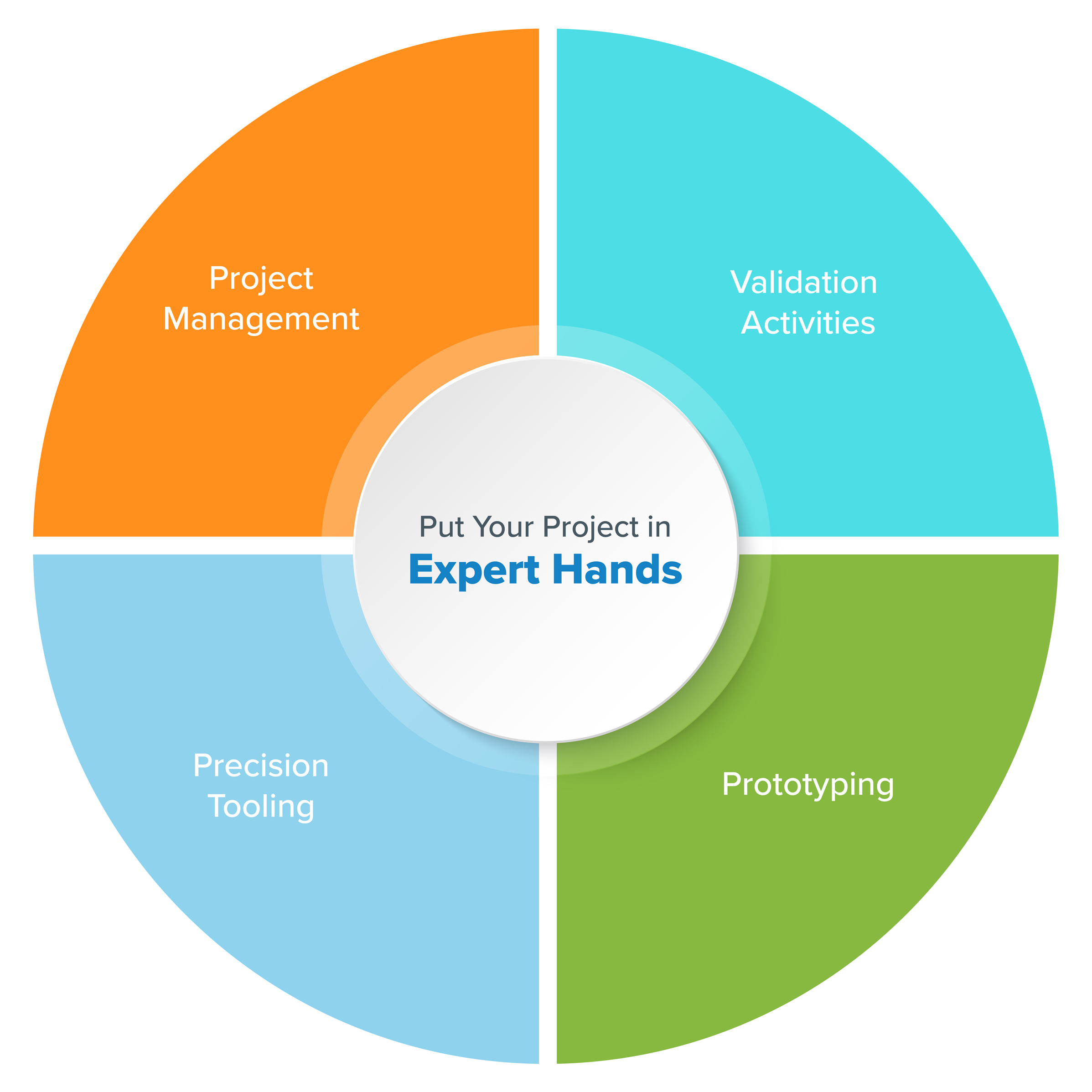
Prototyping
Providing full support from early design stages to complete medical device assembly
CDT’s prototyping process allows you to quickly and effectively test your proof of concept or produce limited volumes for design verification and clinical testing, without incurring the cost and time required for a full production tool. Our dedicated prototype team is available to quickly and accurately prototype your components and requirements.
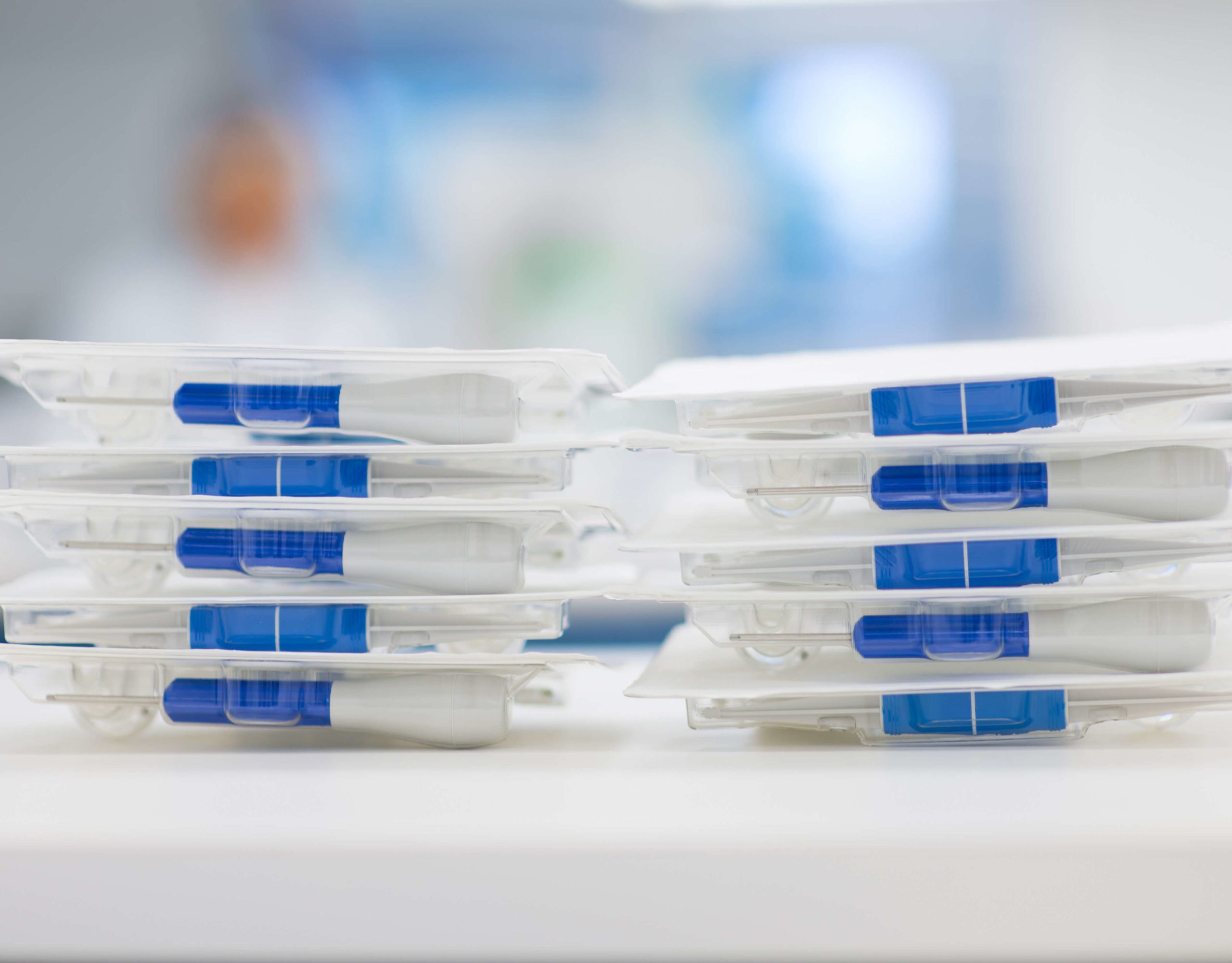
Lorem ipsum:
- Lorem ipsum
- Lorem ipsum
Phased Design Approach
Through our Design for Manufacturability and Assembly (DFMA) process our manufacturing and quality engineering teams work with you to finalize tolerances, design, measurement and verification requirements. This ensures your products can be manufactured to achieve the required performance in the most economical way. We employ Failure Mode Effects Analysis (FMEA) throughout production to ensure we adhere to your production specifications in all possible outcomes.
In regular status meetings led by your project management team, we ensure a mutual understanding of scope and timeline, while identifying and neutralizing obstacles so your project is ready for production on-schedule with a streamlined manufacturing cycle.
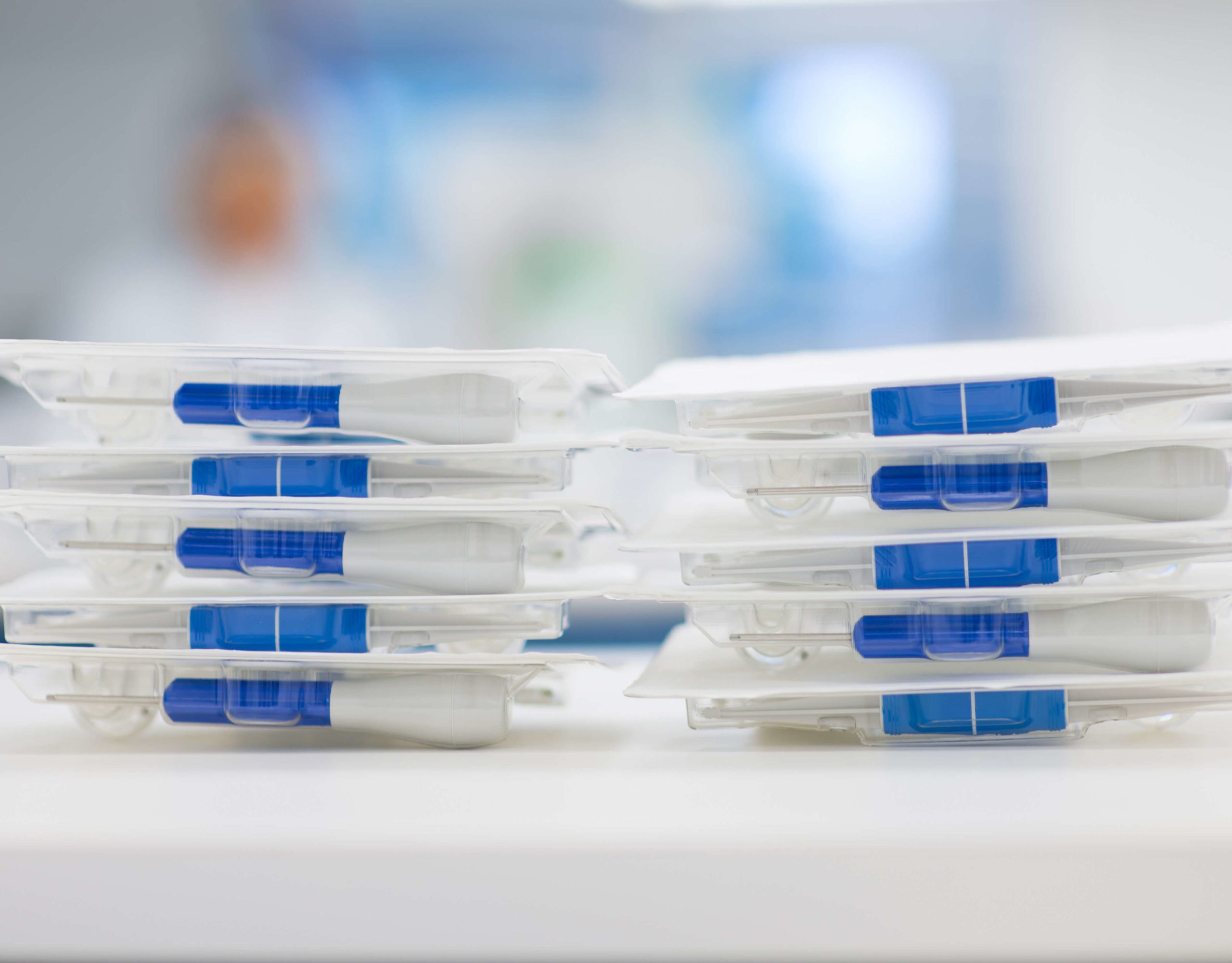
Lorem ipsum:
- Lorem ipsum
- Lorem ipsum
Staged Gate Development Process
For highly complex and multi-faceted programs, our team employs a staged-gate approach to manage product realization from prototype development through product launch. This process ensures you have input and approval every step of the way. We deliver optimal New Product Introduction (NPI) outcomes for our customers by combining experience, expertise and program management.
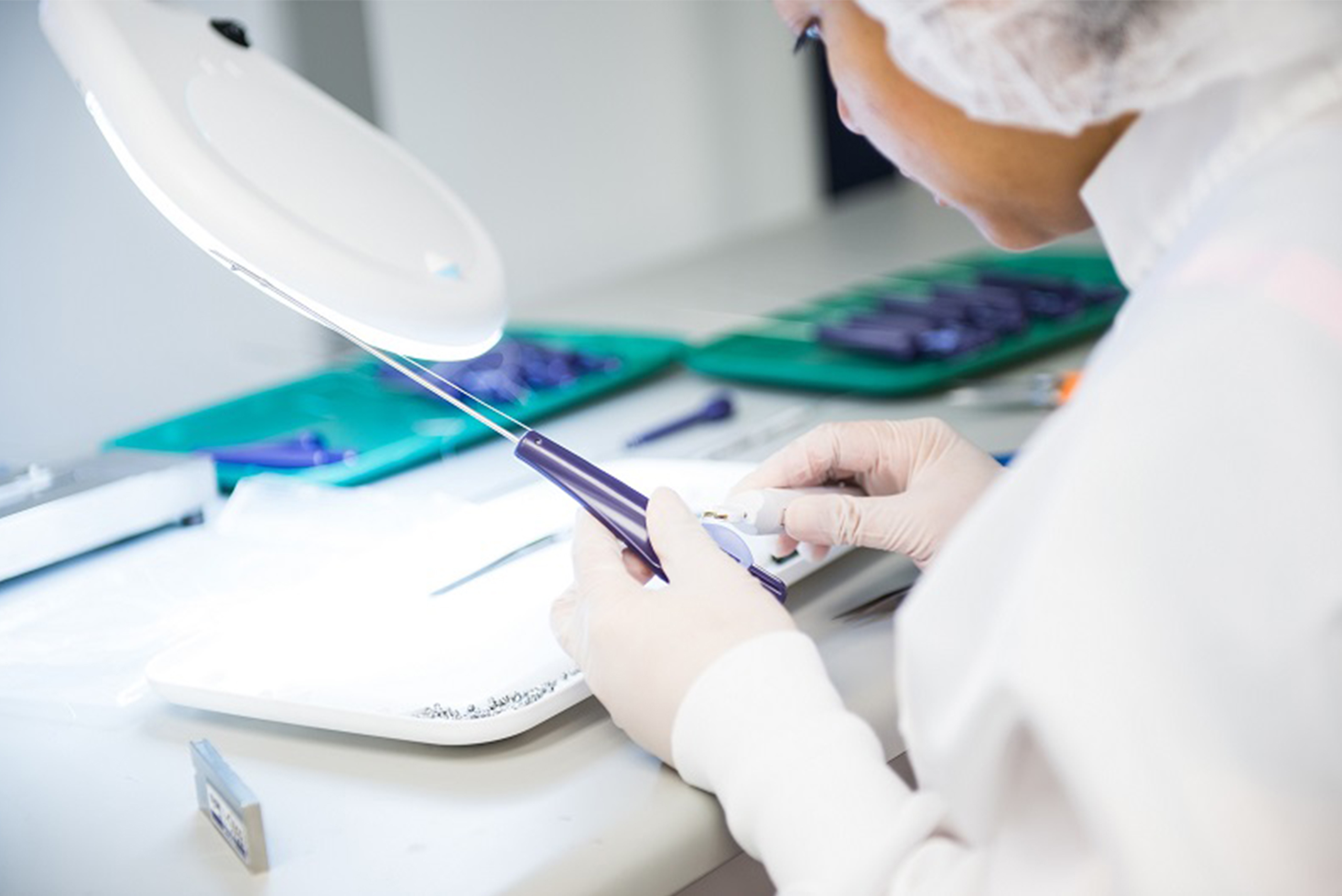
Our Staged Gates:
- Determine Product Requirements
- Support Design Concept Selection
- Product Design Support
- Design Verification Support
- Process Validation (IQ/OQ/PQ, PPAP)
- Transfer to Production
Project Management
Keeping your project on track from beginning to end
We have the expert project managers who can work with you to ensure successful outcomes. With robust validation processes and extensive capabilities, and end-to-end focus, your project is in good hands.
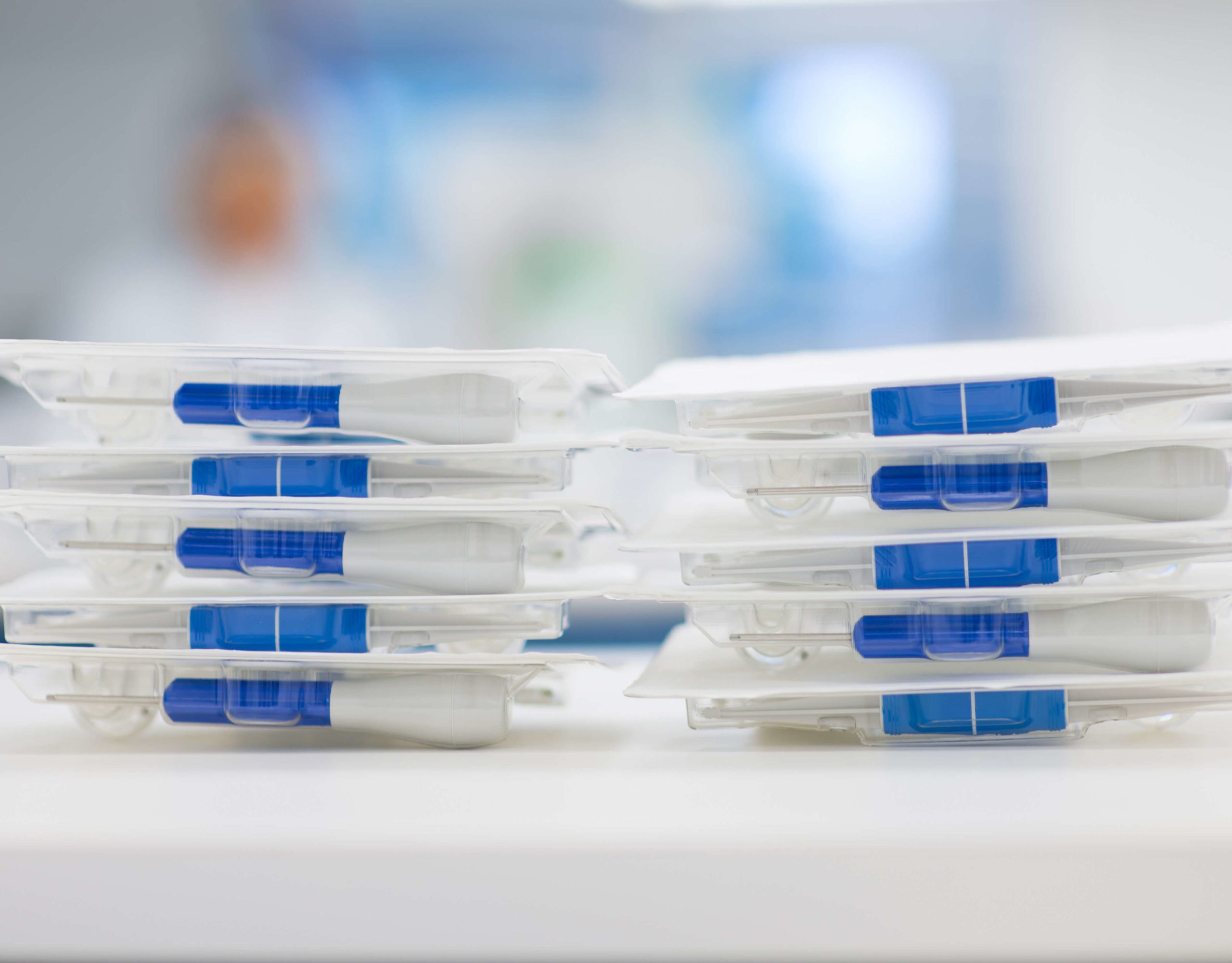
Lorem ipsum:
- Lorem ipsum
- Lorem ipsum
Dedicated Project Team
Well-executed project management is key for the successful launch of your product. Our project managers ensure each project is charting a clear course to deliver your product on time. To facilitate frequent and accurate communication, your team is assigned a dedicated professional to answer your questions, update your project status, and make sure you are always on target.
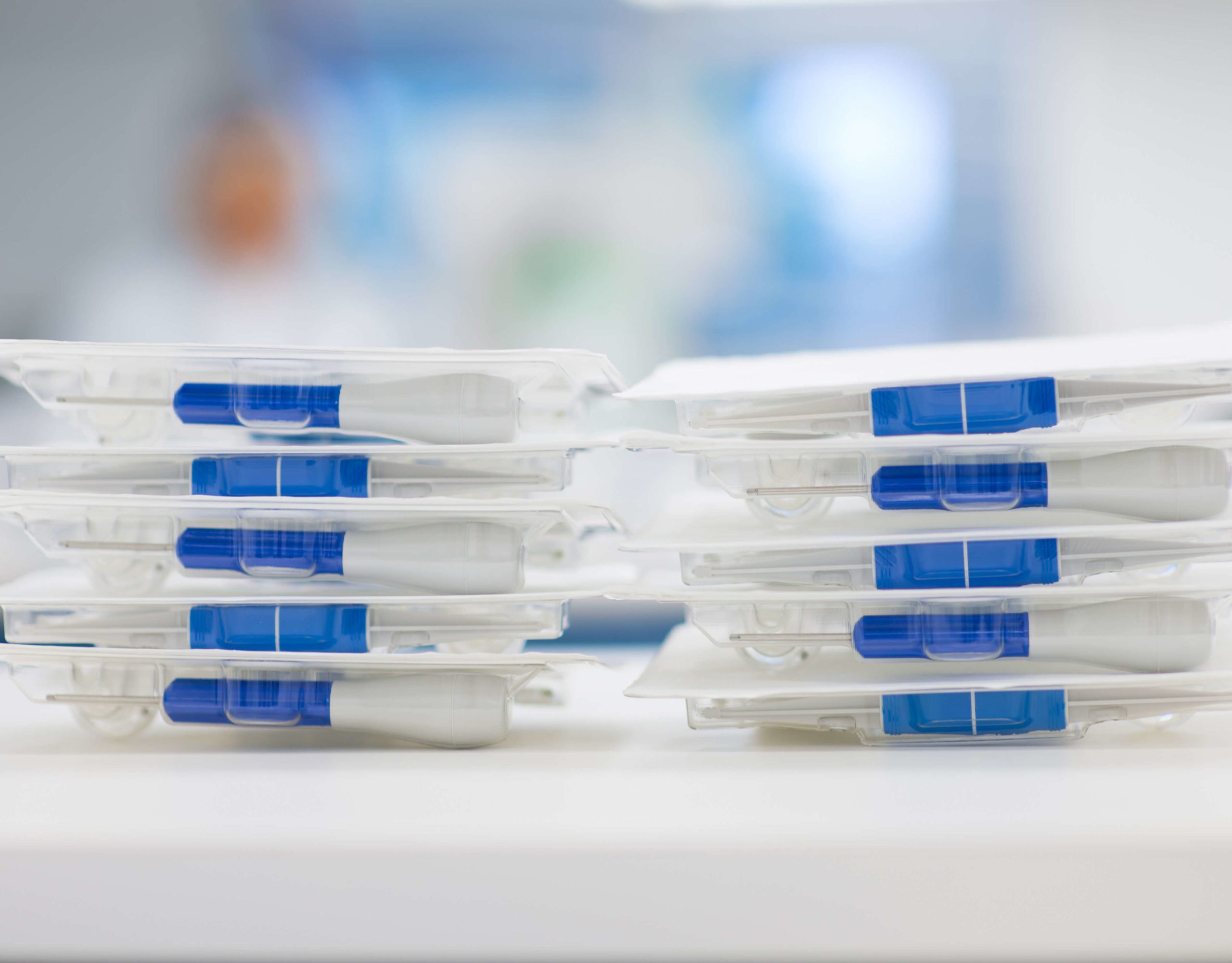
Lorem ipsum:
- Lorem ipsum
- Lorem ipsum
Process Validations
Cretex Medical ensures your medical components and devices meet your exacting requirements by performing thorough validations of our processes. We go beyond just verifying that we are meeting your specifications, we validate our processes, procedures and equipment to make sure we are producing the same quality parts every time.
We validate all aspects of our manufacturing processes from initial tool development, laser processing, molding and stamping of components, to final cleaning procedures. We perform thorough package and sterilization validations to ensure your devices arrive as intended to those who need them.
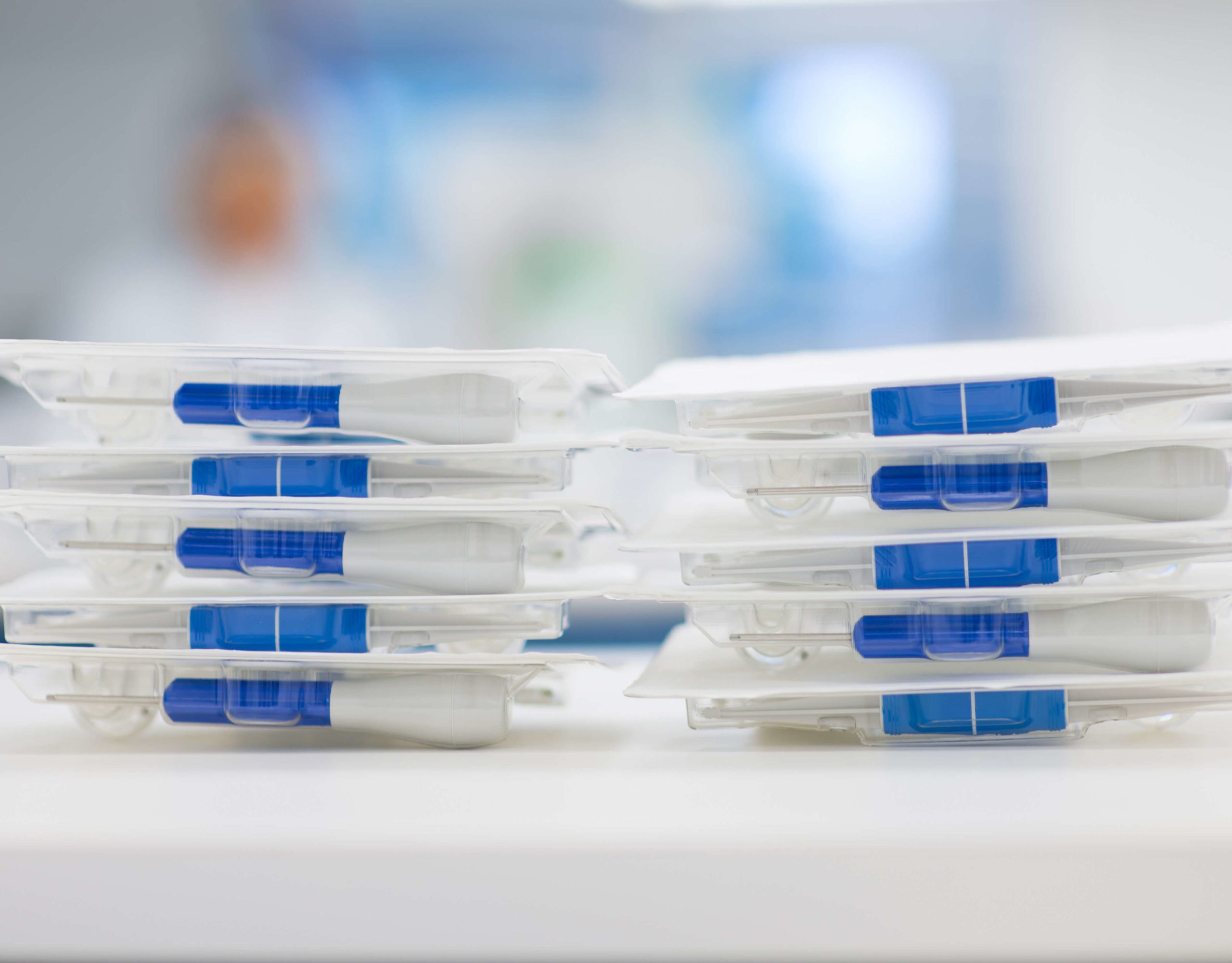
Lorem ipsum:
- Lorem ipsum
- Lorem ipsum
Managing the Supply Chain
Cretex Medical maintains an extensive network of industry-recognized and approved suppliers to increase efficiencies for our customers.
The success of any business hinges on supply chain continuity. We pride ourselves on thoroughly vetting our sub-tier suppliers and holding them to the highest standards. You can rely on us to manage the details of your supply chain, ensuring all your suppliers consistently deliver quality parts on time to keep your project on schedule.
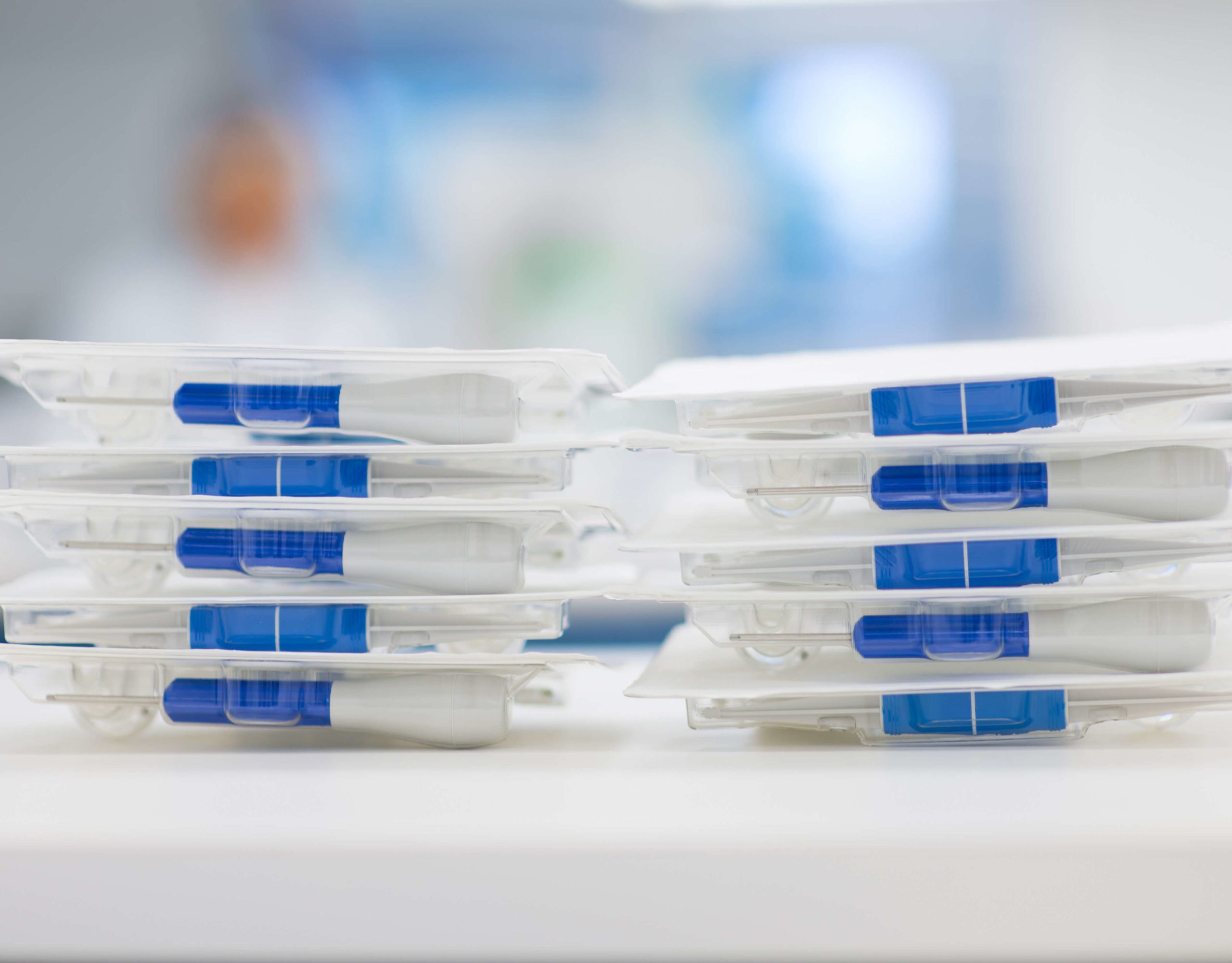
Lorem ipsum:
- Lorem ipsum
- Lorem ipsum
Precision Tooling
Advanced Custom Tooling to Support Your Project’s Needs
To best serve our customers throughout NPI, Transfer and Production projects, Cretex Medical has developed the expertise to fabricate many of the custom molds, dies and tools needed to manufacture your products and components to exacting standards. Maintaining these advanced capabilities in-house accelerates our ability to serve our customers.
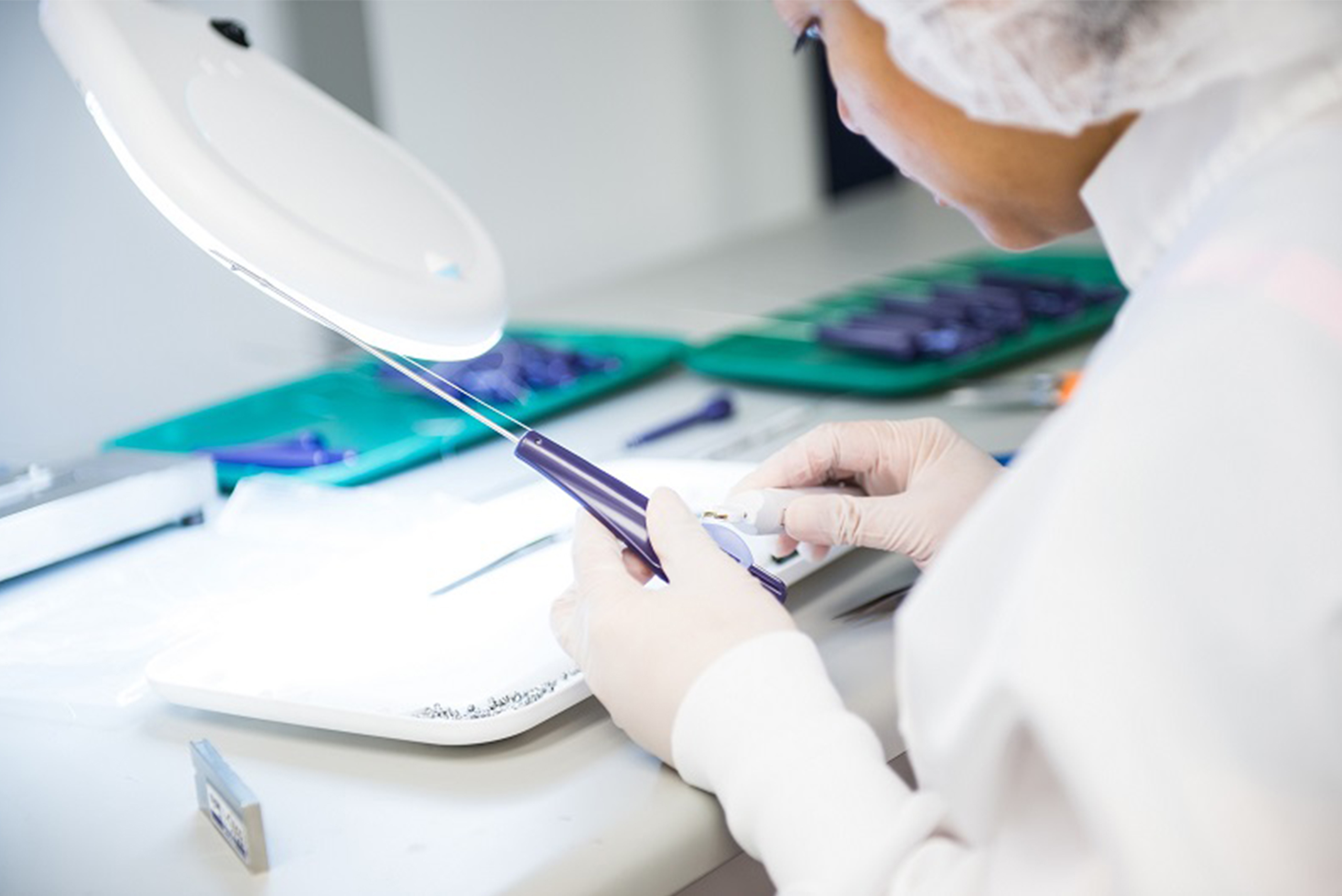
Lorem ipsem:
- Lorem ipsem
- Lorem ipsem
- Lorem ipsem
In-House Tooling Capabilities
Our advanced teams exclusively support your internal tooling requirements. We are equipped with the skills and highly specialized technologies necessary to design, fabricate and maintain the complex tools we use to produce your devices and components.
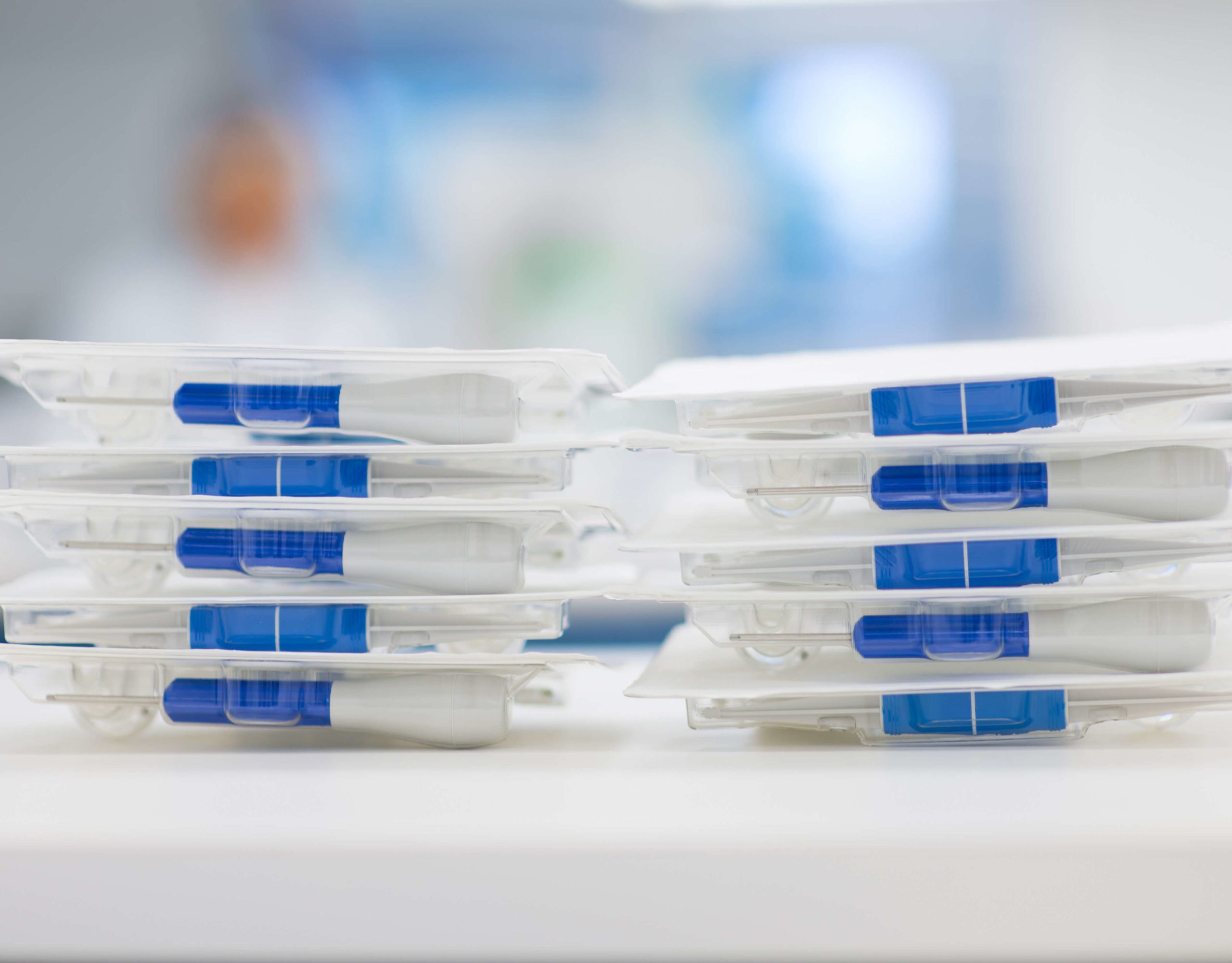
Our state-of-the-art, in-house tooling proficiency includes the ability to design, build and optimize:
- Injection Molds (including multi-shot and insert molds)
- Manufacturing and Assembly Fixtures
- Stamping Dies (progressive, transfer, single station and modular tooling)
- Custom Cutting, Profile and Surface Tools
- Custom Part-specific Inspection Fixtures
- Additive Manufactured Custom Tooling
Tool Maintenance
Molds and dies are maintained at our in-house tooling shops to reduce downtime and ensure they continue to meet the same exacting tolerances established during validation, even after years of production. Through our experience we have mastered material knowledge, intense quality control, and low, medium and high volume applications, all crucial for your successful project outcome.
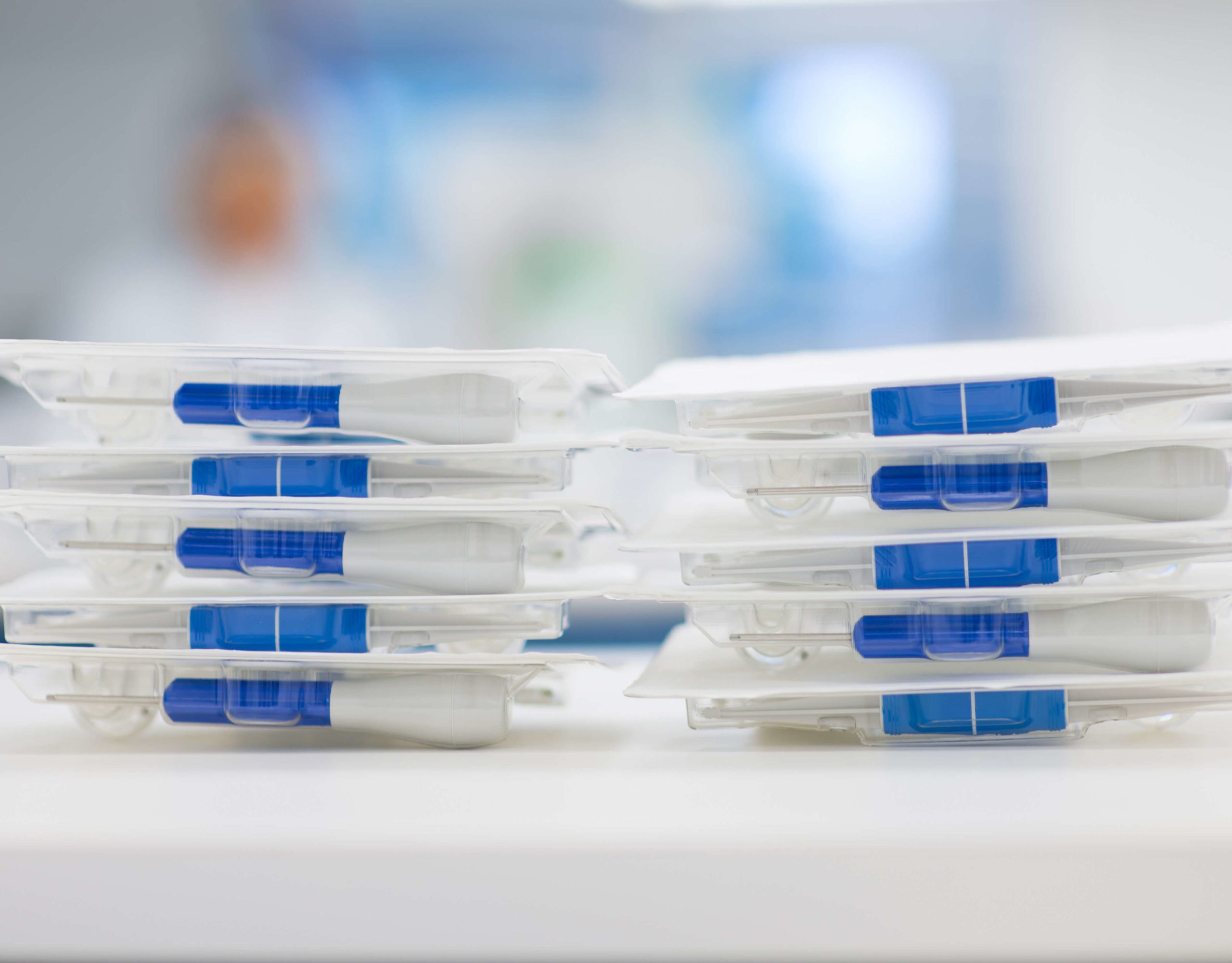
Lorem ipsum:
- Lorem ipsum
- Lorem ipsum
Validation Activities
Our robust validation processes include, but are not limited to:
- Advanced Product Quality Planning (APQP)
- Installation Qualification (IQ)
- Operational Qualification (OQ)
- Performance Qualification (PQ)
- Production Part Approval Process (PPAP)
- Process Failure, Modes, and Effects Analysis (PFMEA)
- Gauge Repeatability and Reproducibility (GR&R)
- Cleaning Validations
- Sterilization Validations
- Package Integrity & Seal Strength Testing
- Package Shelf-Life Studies and Accelerated Aging
- Transportation and Distribution Testing
- Capability Analysis
- Validation Protocol Development
- Statistical Support for Validation Planning and Execution
- Assessment and Leveraging of Product Families