Molding
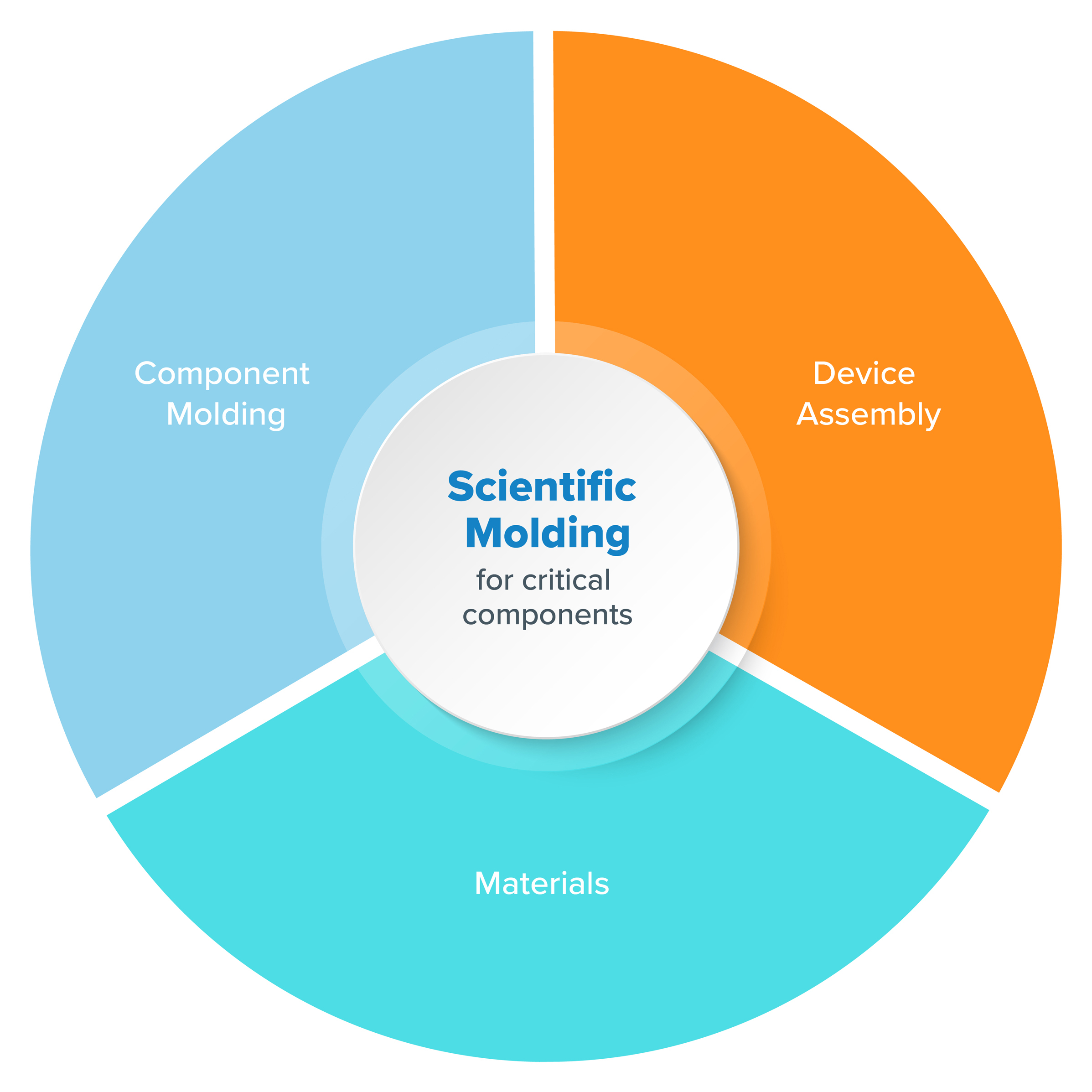
Component Molding
Precision-molded components and assemblies for a wide range of medical devices across multiple markets.
Employing design for manufacturing (DFM) principles, we create effective, repeatable solutions for our customers using the latest technology. We closely monitor critical dimensions and track process controls. Our commitment to meeting rigorous medical industry standards ensures you receive reliable, high-quality component parts.
Technology & Equipment Summary
- 75+ molding presses
- Vertical and horizontal presses
- Press sizes from 20-450 tons
- Mold design, build and maintenance
- Class 7 and Class 8 controlled molding environments
- 70,000 sq. ft. of dedicated manufacturing space
- Dedicated NPI/NPD teams and manufacturing equipment
- Room to expand capabilities and square footage
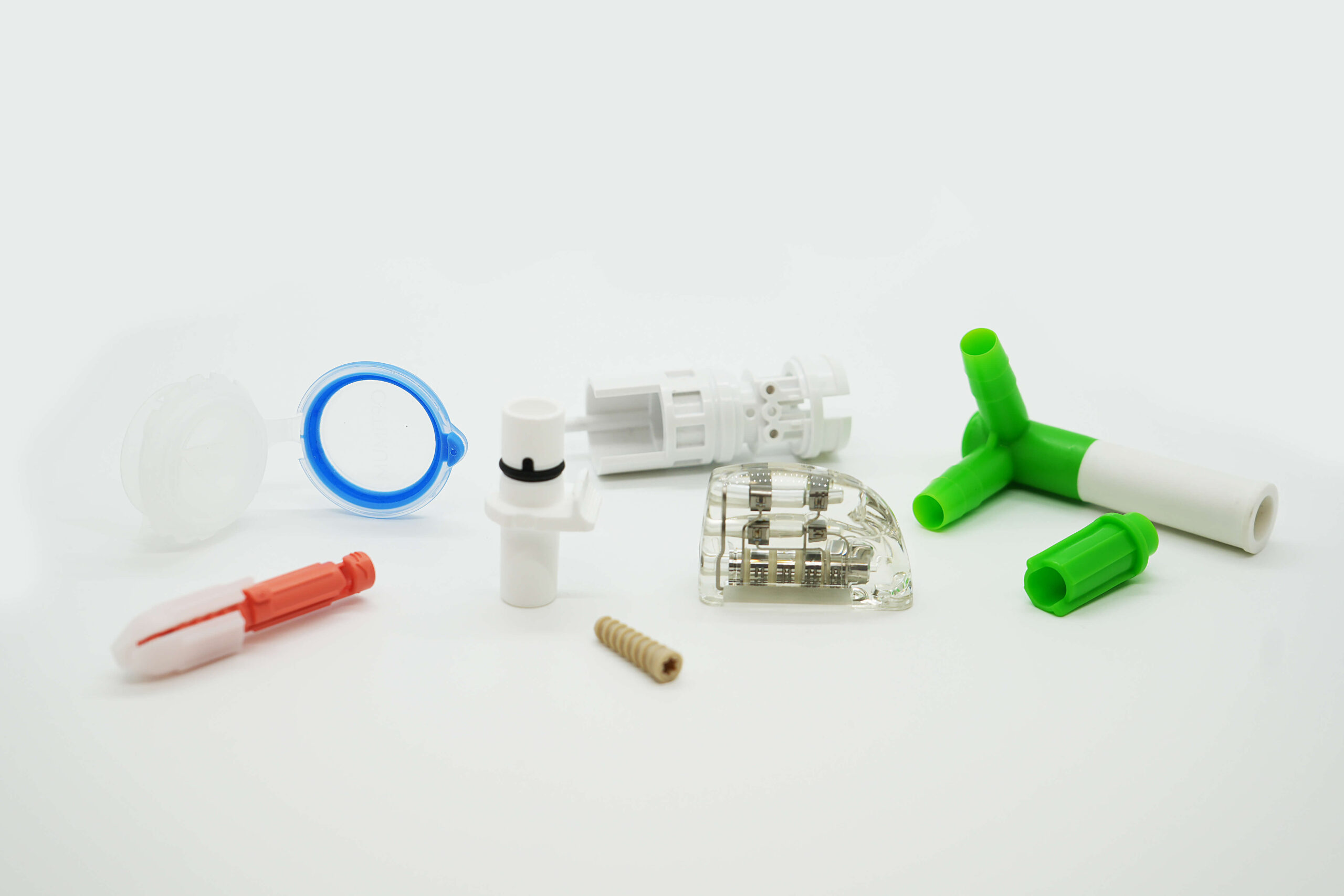
Expert Solutions
Our experts in Insert, Micro, Micro-Insert, and Liquid Silicone techniques make us your go-to partner for medical device molding.
Insert Molding
We specialize in implementing unique strategies, consistent and repeatable loading and unloading methods, and tolerance analysis of over-molded components to maintain proper shut offs and shot-to-shot repeatability.
Capabilities
- Over-molding of metal components such as Nitinol, Platinum or Stainless Steel
- Over-molding 1st shot plastic components with a 2nd shot of the same or different plastic
- Vertical rotating tables to allow additional flexibilities for loading and unloading inserts
- Tight stack up tolerance controls for components produced across the Cretex Medical family of companies
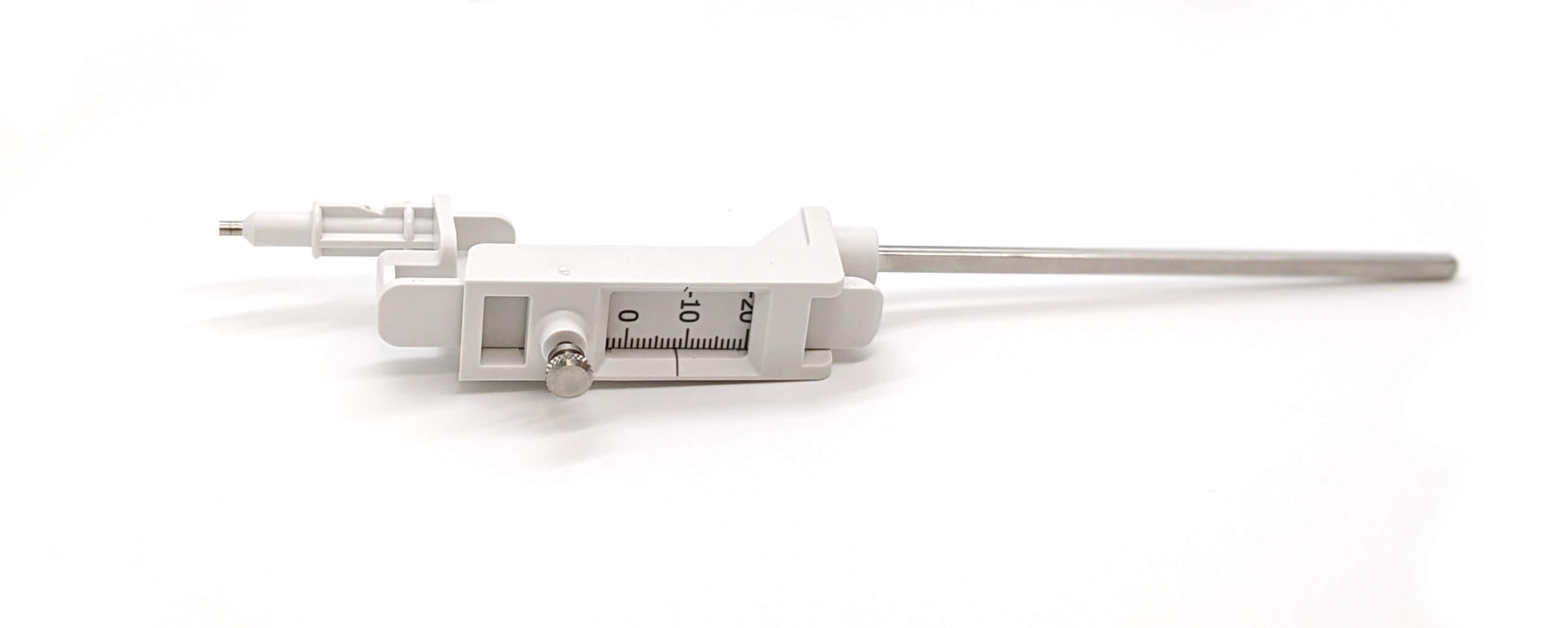
Applications
- Surgical instrument handles
- Headers for cardio and neuro devices
Micro Molding
We have the expertise to meet the unique challenges of extremely small tolerances coupled with process validations that come with molding microscopic medical parts.
Capabilities
- Part sizes as small as <0.001 grams
- Tight tolerance control on micro features
- Design for manufacturing around gate and ejection
- Features <100 microns
- Shot-to-shot repeatability of micro features using micro injection molding machines
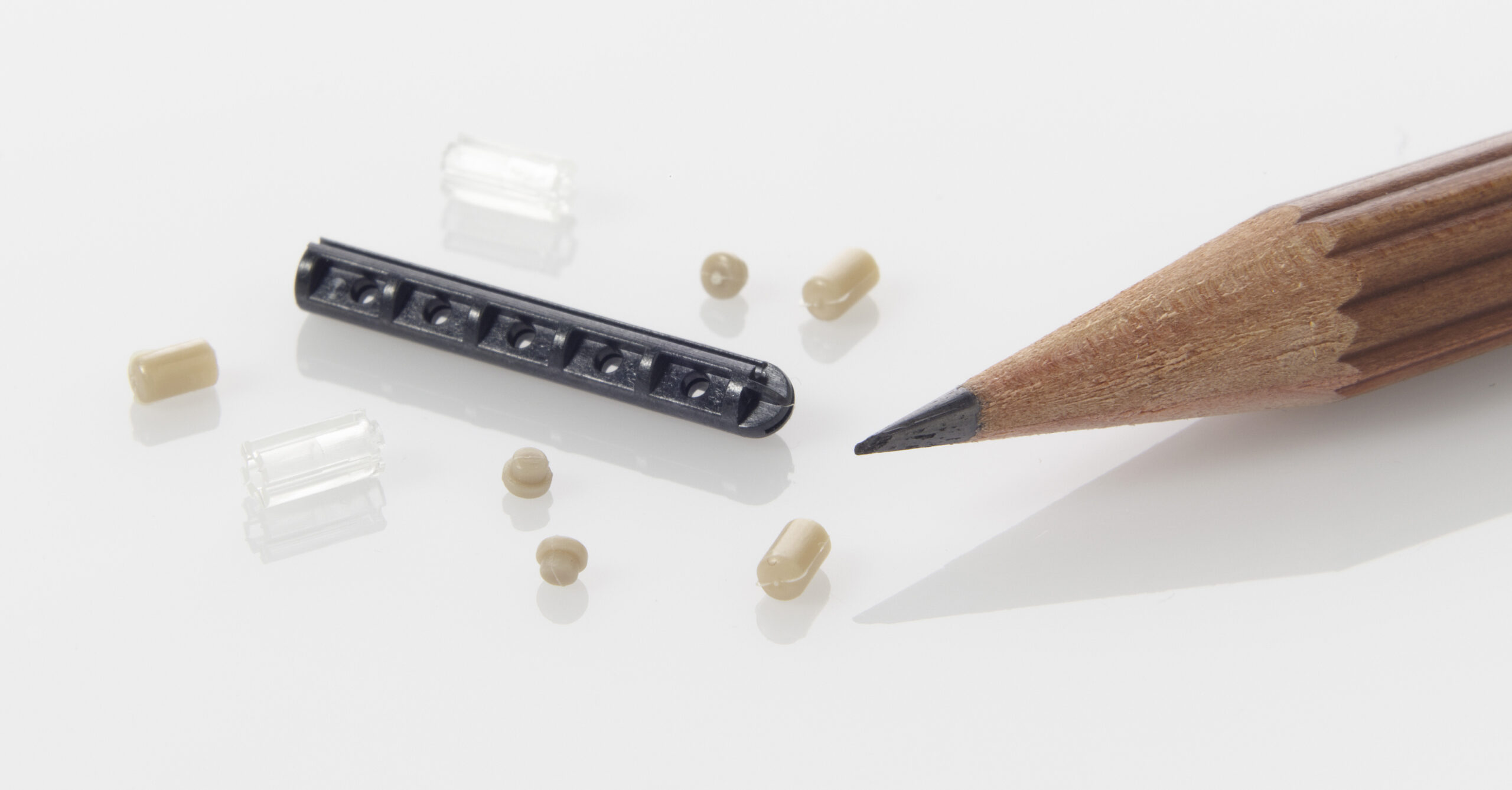
Applications
- Bone screws and implants
- Diagnostic implants
Micro-Insert Molding
Our investment in technology, and our advanced engineering approach, leads to shot-to-shot repeatability of micro-insert molding. We can produce very small components with complex geometries, including threads, plunging/bulkheads and holes to meet exacting requirements.
Capabilities
- In-source micro inserts for overmolding by leveraging the capabilities across the Cretex Medical family
- Tight tolerance control for shut off locations due to insourcing
- Internal automation for loading inserts with less labor and more consistent cycles
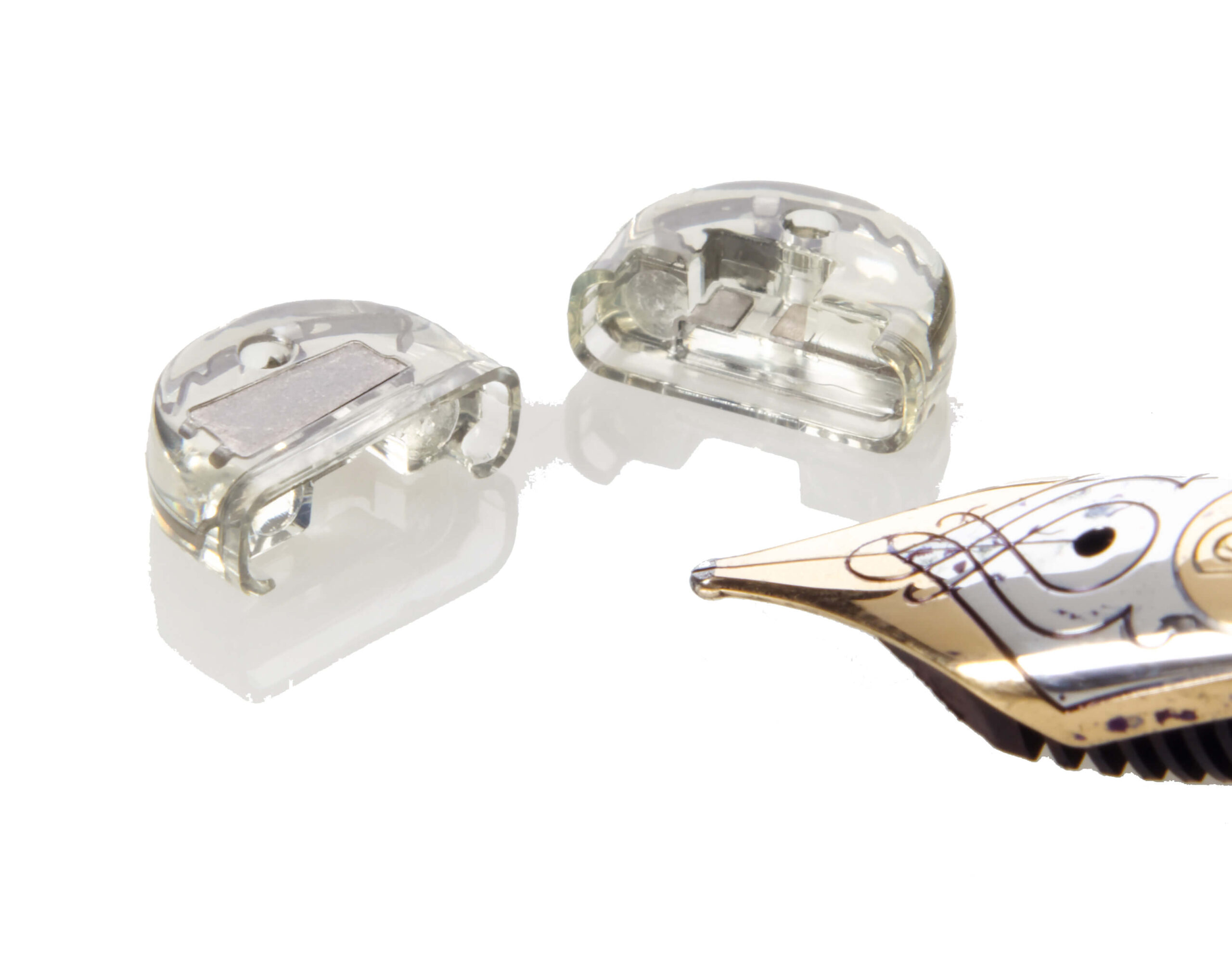
Applications
- Leads for Deep Brain Stimulation (DBS) leads
- Diagnostic implants
Liquid Silicone Molding
When you need excellent biocompatibility, high tensile strength, low compression set, chemical inertness, durability and sterilization compatibility, our silicone molding facilities are the right choice.
Capabilities
- 20 to 40 ton vertical
- 100 ton horizontal
- Individual components to fully integrated over-molded sub-assembly
- Semi-auto to fully automated cells
- Implantable and non-implantable LSR
- Traditional LSR over-molding with micro-molding capabilities
- Material range 20-90A durometers
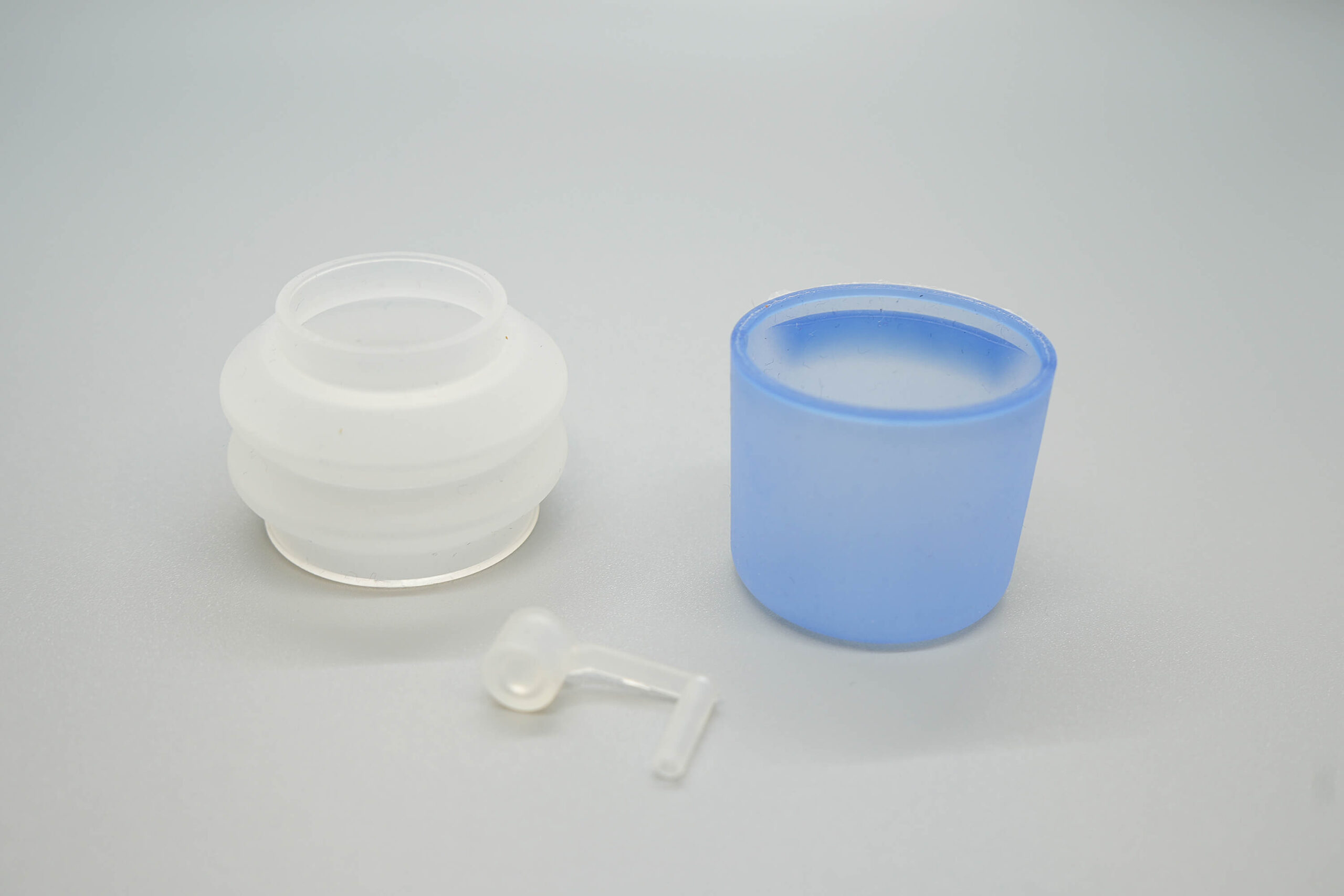
Applications
- Seals for cardio and neurovascular devices
- Balloons
- Surgical jaws
- Leads for neurostimulation devices
Two-Shot Molding
Our two-shot technology gives you increased freedom in part design, so you’re not limited by assembly requirements. Two-shot molding improves quality and consistency by reducing misalignments that can result from traditional insert or over molding processes. It also eliminates the costs of additional operations, assembly and extra tool validation.
Capabilities
- Rotary two-shot machines up to 220-tons
- In-mold spin stack technology with auxiliary injection units
- Pick and place transfer two-shot capabilities for complex two-shot insert molding products
- In-house automation for complex two-shot applications
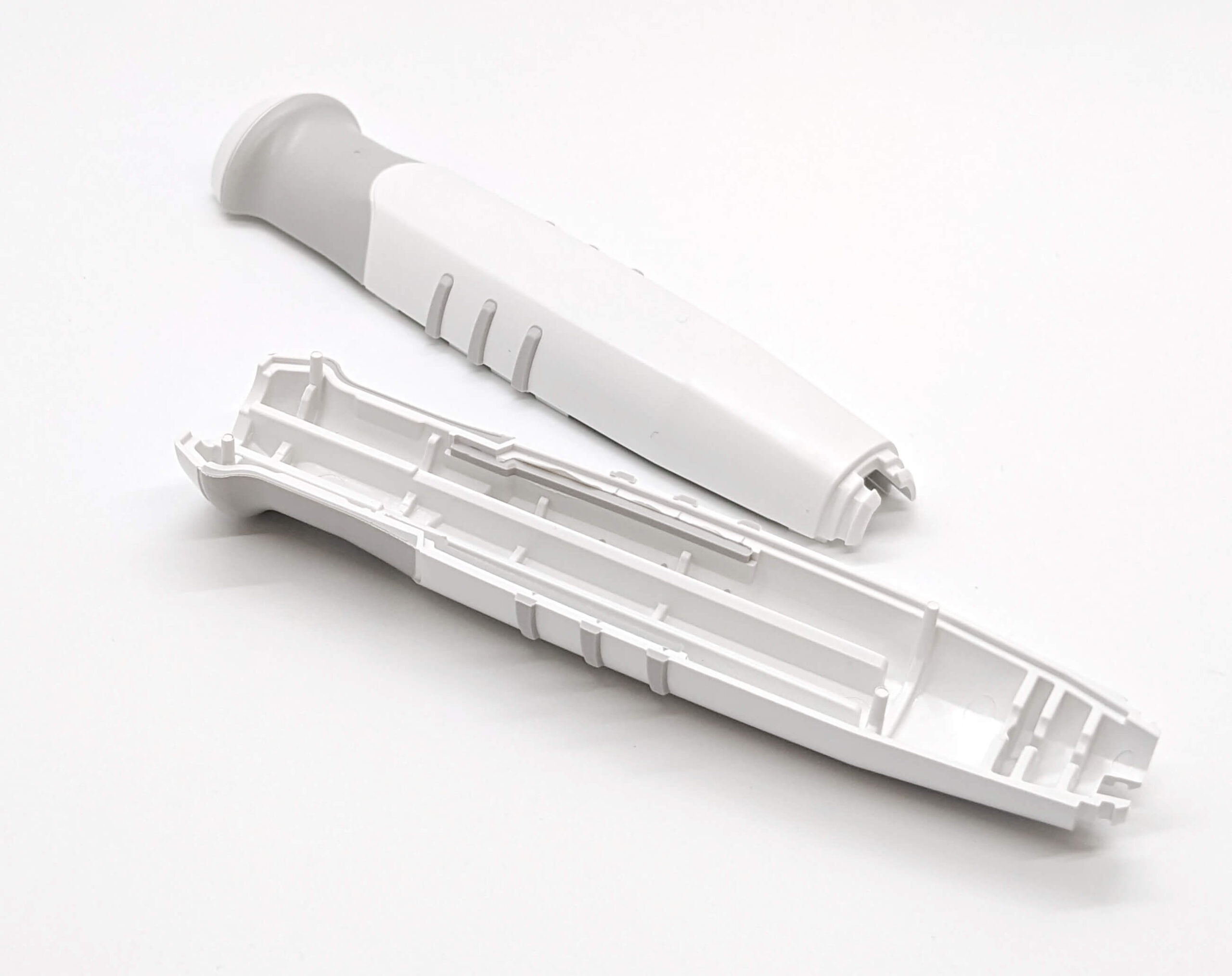
Applications
- Grips on surgical tools and instruments
- Slitter blades
- Instrument handles
- Connectors
Device Assembly
Assembling medical devices efficiently and effectively.
We manufacture a wide range of devices including orthopaedic and surgical instruments, ophthalmic surgical interfaces, and critical header and lead subassemblies for cardiac rhythm management and neuromodulation devices. Our facilities observe strict GMP adherence and employ ISO 13485 quality management.
Our highly trained employees work in cleanrooms equipped with cutting-edge technology for manufacturing and assembly of sterile medical devices and components.
Capabilities
- FDA registered facilities clean room assembly in both Class 7 and Class 8 environments
- Manufacturing Process Failure Mode and Effect Analysis (PFMEA)
- Tensile, torque and leak (mechanical & electrical) testing
- Sterile device verification and validation (V&V) testing
- Epoxy/UV curing assembly
- Mechanical assembly
- Subassembly and finished device assembly
- Heat staking and ultrasonic welding
- Laser and resistance welding
- Pad printing and decorating
- Part pouching and sealing
- Complete kitting, packaging, and labeling
- Sterilization management
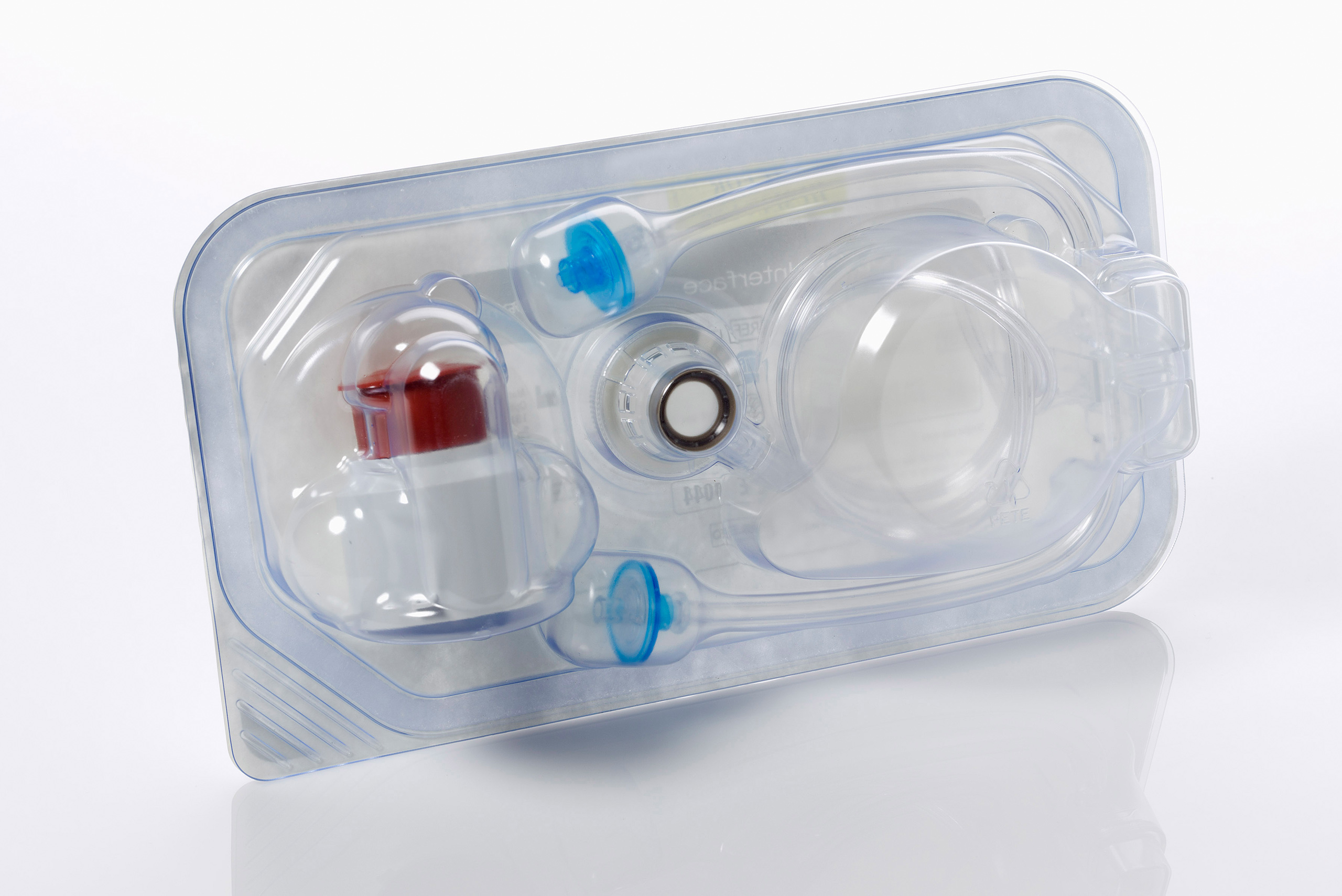
Device Applications
- Single-use surgical kits
- Drug delivery kits
- Endoscopic tools
Materials
Ensuring safety and effectiveness of medical devices through diligent material selection.
With extensive injection molding experience, we have developed advanced capabilities across a wide range of medical grade polymers. We employ applied understanding of material properties and molding characteristics coupled with the latest mold flow analytical tools to optimize tooling for reduced variability, maintained tolerances, extended tool life, and controlled costs. Our practical knowledge of how materials behave during the molding process is applied during the Design for Manufacturability (DFM) process, ensuring optimal outcomes in device design.
Among the thousands of resins we use are:
- ABS
- Acetal
- Acetal copolymers – Ultem® (PEI)
- Bionate II
- Crystal styrene
- GF Nylon
- HDPE
- LC
- PEEK
- Bioactive PEEK (Proprietary)
- Carbon-filled PEEK
- Commercial grade PEEK (450G / 150G) Short term exposure and suitable for molding process development
- PEEK Optima (LT1 / LT3) Long term Implant
- Glass-filled PEEK
- Nylon
- 101L Nylon
- Nylon 6/6
- Polycarbonate
- Polystyrene
- Polysulfone
- Polyurethanes (Implant Grade)
- Elasthane
- Tecothane
- Pellethane
- PP
- Radel
- Stanyl
- UHMWPE